Optimizing AP in manufacturing: Streamlining invoice processes for large-scale production
Efficient accounts payable (AP) processes are crucial for success in today's manufacturing landscape. As manufacturing companies navigate fluctuating demand, complex supply chains, and stringent regulations, streamlining invoice processes and enhancing financial accuracy are imperative. In this article, we'll explore the critical role of AP optimization in large-scale production environments, from seamless integration with manufacturing operations to efficient cost allocation and robust supplier management.
Challenges in manufacturing AP processes
Manufacturing companies face unique challenges in their accounts payable (AP) processes due to the complexities inherent in their operations. In comparison to other industries, such as services or retail, manufacturers must contend with a range of factors that impact their AP efficiency and accuracy.
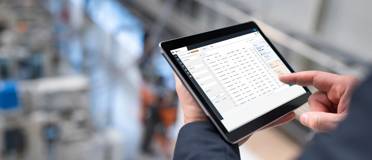
Invoice processing complexity
Managing invoices in manufacturing involves handling a high volume of transactions from diverse suppliers, each with its unique requirements and formats. The complexity of invoice processing often leads to delays, errors, and inefficiencies, hampering the overall AP workflow. To streamline invoice processing, manufacturing companies can leverage advanced automation tools, digitize manual processes, and implement centralized management systems.
Solutions
Automation tools: Deploying AP automation software can automate repetitive tasks, such as data entry and invoice routing, reducing manual errors and accelerating processing times.
Digitization: Transitioning from paper-based to electronic invoices enables faster document handling, improves data accuracy, and enhances accessibility.
Centralized management systems: Implementing a centralized invoice management system provides visibility into the entire invoice lifecycle, streamlines approval workflows, and facilitates collaboration between departments and suppliers.
Benefits
Increased efficiency: Automation streamlines invoice processing workflows, enabling AP teams to handle large volumes of invoices with greater speed and accuracy.
Cost savings: By reducing manual labor and eliminating paper-based processes, companies can achieve significant cost savings and allocate resources more effectively.
Enhanced compliance: Centralized management systems ensure adherence to regulatory requirements, audit standards, and internal policies, reducing the risk of non-compliance and associated penalties.
Seasonal demand fluctuations
Seasonal demand fluctuations pose a significant challenge for manufacturing companies, leading to unpredictable spikes or dips in invoice volumes. During peak seasons, AP departments may struggle to process invoices promptly, resulting in payment delays and strained supplier relationships. Conversely, off-peak periods may lead to underutilization of AP resources, causing inefficiencies and increased processing times.
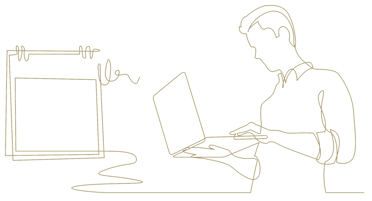
Solutions
Capacity planning: Forecasting demand fluctuations enables AP departments to allocate resources effectively, ensuring sufficient staffing levels during peak periods and optimizing resource utilization during off-peak seasons.
AP automation: Implementing AP automation solutions allows companies to scale invoice processing capacity dynamically, leveraging automation tools to handle fluctuating invoice volumes efficiently.
Supplier collaboration: Building strong relationships with suppliers and communicating proactively about anticipated demand fluctuations can help mitigate issues related to invoice processing delays and payment disputes.
Benefits
Improved cash flow: Proactive capacity planning and automation enable companies to manage cash flow effectively during periods of high demand, ensuring timely invoice processing and payment disbursement.
Enhanced supplier relationships: Transparent communication and efficient invoice processing during peak seasons foster trust and collaboration with suppliers, strengthening long-term partnerships.
Operational flexibility: Agile AP processes equipped to handle seasonal demand fluctuations enhance operational resilience and adaptability, enabling companies to respond effectively to market dynamics.
Inventory management integration
Integrating AP processes with inventory management systems presents a challenge for manufacturing companies, as it requires seamless coordination between finance and operations departments. Inaccurate inventory data or discrepancies between AP and inventory records can result in errors in invoice processing, inventory valuation, and financial reporting. Additionally, manual reconciliation of invoices with inventory receipts and supplier contracts can be time-consuming and prone to errors.
Solutions
ERP integration: Leveraging enterprise resource planning (ERP) systems that integrate AP and inventory management modules facilitates real-time data synchronization and streamlines invoice reconciliation processes.
Automated reconciliation: Implementing automated reconciliation tools enables AP departments to match invoice data with inventory receipts and supplier contracts, reducing manual effort and improving accuracy.
Supplier collaboration: Collaborating closely with suppliers to reconcile invoices with inventory deliveries and resolve discrepancies promptly enhances data accuracy and reduces invoice processing delays.
Benefits
Enhanced data accuracy: Integrating AP processes with inventory management systems ensures consistency and accuracy in inventory data, leading to more reliable financial reporting and decision-making. By eliminating data discrepancies and errors, companies can make informed business decisions and optimize inventory levels effectively.
Streamlined processes: Automated reconciliation tools and ERP integration streamline invoice processing and inventory management workflows, reducing cycle times and improving operational efficiency. By automating repetitive tasks and eliminating manual reconciliation efforts, companies can allocate resources more effectively and focus on strategic initiatives.
Cost savings: Reduced manual effort and improved data accuracy result in cost savings associated with invoice processing, inventory management, and financial reporting. By optimizing AP processes and streamlining inventory-related workflows, companies can minimize operational costs and improve profitability.
Managing supplier relationships
Manufacturing companies often rely on a vast network of suppliers to procure raw materials, components, and services essential for their production processes. However, managing these supplier relationships can present several challenges, including communication barriers, quality control issues, and payment discrepancies.
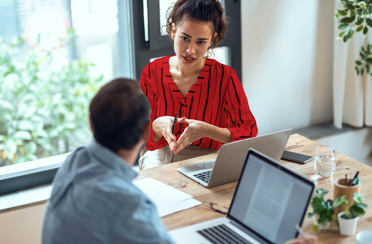
Solutions
Supplier collaboration platforms: Implementing collaboration platforms facilitates communication and collaboration between manufacturers and suppliers. These platforms enable real-time interaction, document sharing, and issue resolution, fostering stronger relationships and enhancing transparency.
Quality management systems: Integrating quality management systems into the supplier relationship management process ensures adherence to quality standards and specifications. By monitoring and tracking supplier performance metrics, manufacturers can identify areas for improvement and address quality issues proactively.
Performance monitoring tools: Utilizing performance monitoring tools allows manufacturers to track key performance indicators (KPIs) and evaluate supplier performance objectively. By establishing clear performance metrics and benchmarks, companies can incentivize suppliers to meet or exceed expectations.
Benefits
Improved supplier relationships: Effective supplier management fosters trust, collaboration, and mutual understanding, leading to stronger and more reliable supplier relationships.
Enhanced product quality: By ensuring consistent quality standards across their supply chain, manufacturers can deliver high-quality products to their customers, enhancing brand reputation and customer satisfaction.
Navigating tax complexity
Manufacturing companies operate within a complex tax landscape characterized by diverse regulations, varying tax rates, and evolving compliance requirements across different jurisdictions. Navigating these complexities poses challenges for accounts payable (AP) departments, leading to potential errors, compliance risks, and financial penalties. To address these challenges effectively, manufacturing companies can adopt several solutions and strategies:
Solutions
Tax compliance automation: Implementing tax compliance automation tools helps AP departments stay updated on tax regulations, calculate taxes accurately, and ensure compliance with local tax laws. By automating tax-related processes, companies can minimize errors, reduce compliance risks, and streamline tax reporting requirements.
Vendor tax validation: Verifying vendor tax information and validating tax IDs ensures that invoices are processed accurately and in compliance with tax regulations. By implementing automated vendor tax validation processes, companies can identify discrepancies, prevent fraudulent activities, and mitigate tax compliance risks effectively.
International tax expertise: Leveraging the expertise of tax professionals with knowledge of international tax regulations and cross-border transactions is essential for navigating complex tax issues. By partnering with tax advisors or consultants, companies can ensure compliance with global tax requirements, minimize tax liabilities, and optimize tax planning strategies.
Benefits
Reduced compliance risks: Automation tools and vendor tax validation processes help companies identify and address compliance issues proactively, reducing the risk of non-compliance and associated penalties. By ensuring accurate tax calculations and adherence to regulatory requirements, companies can mitigate compliance risks and maintain financial integrity.
Improved efficiency: Tax compliance automation streamlines tax-related processes, such as tax calculation, reporting, and documentation, reducing manual effort and accelerating workflow efficiency. By automating repetitive tasks and eliminating manual errors, companies can optimize AP operations, increase productivity, and free up resources for strategic initiatives.
Enhanced cost savings: Effective tax management and compliance automation result in cost savings by reducing the need for manual intervention, minimizing compliance-related penalties, and optimizing tax planning strategies. By optimizing tax processes and leveraging automation tools, companies can achieve significant cost savings and improve overall financial performance.
Streamlining AP processes with Medius
In the dynamic world of manufacturing, efficient accounts payable processes are crucial for operational agility and financial stability. Medius offers tailored AP automation solutions to address challenges like invoice processing complexities, seasonal demand fluctuations, and supplier relationship management.
Our solutions empower manufacturing companies to automate invoice processing, optimize capacity planning, and strengthen supplier relationships. With Medius, organizations can achieve greater efficiency, transparency, and control in their AP operations, enabling them to focus on innovation and staying competitive in today's market.
Contact us today to learn how Medius can transform your AP processes and drive success in manufacturing.
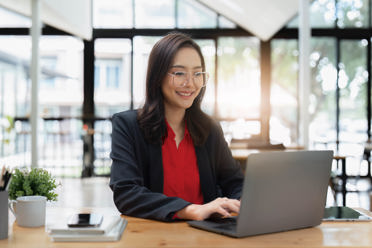